Understanding the Basics of Hydraulic Systems and Their Applications
- Kay Quickfall
- Jun 4
- 3 min read
Updated: Jun 27
Hydraulic systems play a crucial role in various industries. From construction machinery to manufacturing applications, these systems harness the power of fluids to generate force. In this blog post, we will explore the fundamental principles of hydraulic systems, their components, and the range of applications where they are employed.
What Are Hydraulic Systems?
Hydraulic systems operate using fluids, typically oil or water, to transmit power. They rely on Pascal's principle, which states that pressure applied to a confined fluid is transmitted undiminished throughout the fluid. This fundamental principle allows hydraulic systems to create significant force with minimal input.
Components of Hydraulic Systems
To understand hydraulic systems, it's essential to know their key components:
Hydraulic Fluid: The medium through which power is transmitted. It must have specific properties, such as low viscosity and good lubricating qualities.
Pumps: These devices convert mechanical energy into hydraulic energy. Common types include gear pumps, vane pumps, and piston pumps.
Actuators: These are devices that convert hydraulic energy back into mechanical motion. Cylinders and motors are examples of actuators.
Valves: Valves control the flow and direction of hydraulic fluid within the system.
Reservoirs: These store hydraulic fluid and allow for expansion, enabling the system to maintain a consistent pressure.
Filters: Filters are crucial for maintaining the cleanliness of hydraulic fluid, preventing contamination that can lead to system failure.
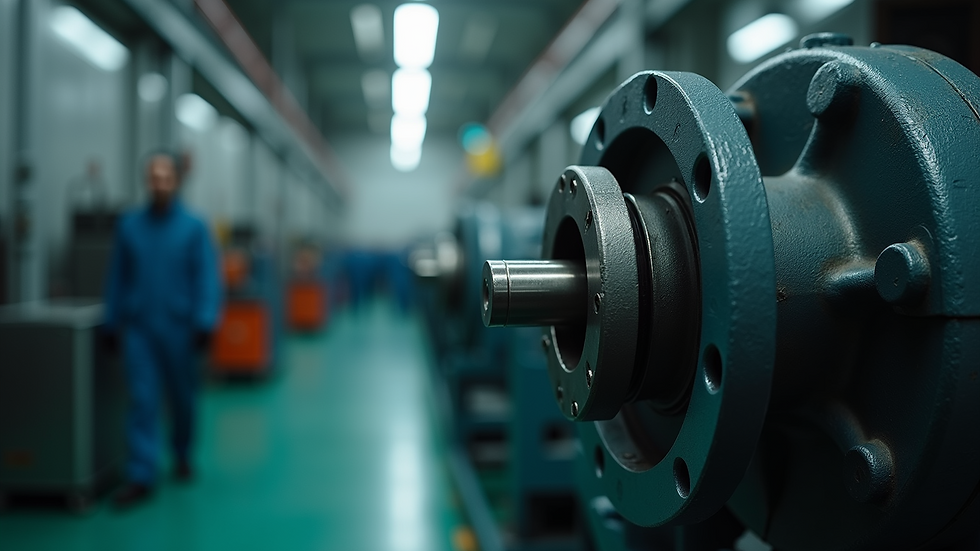
The Functionality of Hydraulic Systems
Hydraulic systems function by converting energy from a pump into fluid power. When the pump pushes hydraulic fluid into the system, it creates pressure. This pressure can then be directed to various actuators throughout the system.
For instance, in construction equipment, hydraulic systems are commonly used to lift heavy loads. A small amount of force applied at the pump generates a much larger force through the cylinder. This mechanical advantage is what makes hydraulic systems so powerful.
Advantages of Hydraulic Systems
Hydraulic systems have several advantages over mechanical systems:
High Power Density: They can produce a significant amount of power in a compact form.
Precision Control: Hydraulic systems allow for precise movement and control.
Simplicity: The design of a hydraulic system can be simpler than mechanical equivalents.
Durability: Hydraulic components are generally robust and can withstand harsh environments.

Applications of Hydraulic Systems
Hydraulic systems are extensively used across various industries. Here are some notable examples:
Construction and Excavation: Hydraulic systems power excavators, bulldozers, and cranes, enabling them to lift and move heavy materials.
Manufacturing: Hydraulic presses are used to shape materials and components in automotive and aviation manufacturing.
Aerospace: In aircraft, hydraulic systems control landing gear, brakes, and flight control surfaces.
Automotive: Hydraulic brakes in vehicles rely on hydraulic fluid to provide stopping power, enhancing safety and efficiency.
Agriculture: Tractors and harvesting equipment utilize hydraulic systems for lifting and steering, improving productivity on farms.
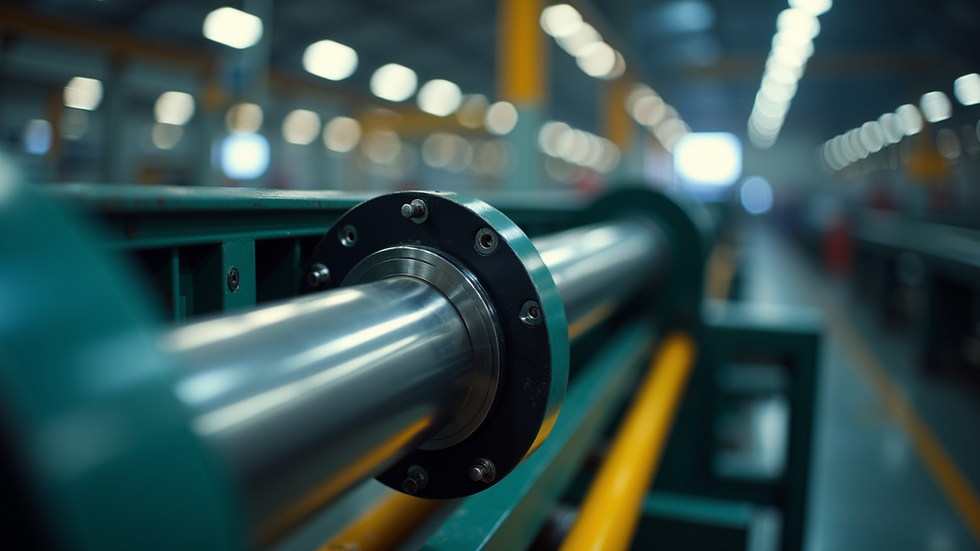
Maintenance of Hydraulic Systems
Regular maintenance of hydraulic systems is essential for long-lasting performance. Here are some key practices:
Check Fluid Levels: Ensure that hydraulic fluid levels are always optimal. Inadequate fluid can lead to system failure.
Inspect for Leaks: Regularly check all connections and hoses for leaks. Any fluid loss can severely impact the system's performance.
Change Filters: Clean or replace filters to maintain fluid cleanliness, preventing contamination.
Monitor Temperature: Excessive heat can degrade hydraulic fluid and damage components. Use temperature sensors to keep checks on system temperature.
Gauge Performance: Regularly test the system to ensure it operates within specified parameters. Monitoring pressure and flow can help identify potential issues early.
The Future of Hydraulic Systems
As technology progresses, hydraulic systems are evolving. Innovations such as smart sensors and IoT integration are enhancing the control and efficiency of hydraulic systems. Automation is also becoming common, reducing the need for manual labor and improving safety conditions.
Additionally, hydraulic systems are increasingly using biodegradable fluids to address environmental concerns. This shift will not only provide the necessary power but also reduce the ecological impact of hydraulic leaks.
In conclusion, hydraulic systems are a vital part of many industries, thanks to their ability to generate powerful movement efficiently. Understanding their workings, benefits, and applications can help businesses optimize their use, leading to enhanced performance and productivity. If you're seeking reliable hydraulic equipment, consider visiting BVA Hydraulic for high-quality solutions tailored to your needs.
As you delve deeper into the world of hydraulics, always keep in mind the significance of maintenance and innovation to ensure your systems remain effective and sustainable.
Comments